Ультразвуковой контроль сварных соединений
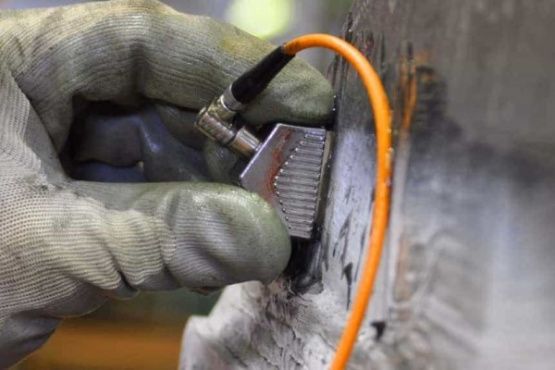
С первой трети ХХ в. специалистам удалось разработать методы эхолокации и теперь ультразвуковая дефектоскопия применяется для обнаружения дефектов сварных швов. Она помогает выявлять нарушения химического состава наплавки, замечать появление оксидных соединений, обнаруживать наличие шлаков или определять надежность их слоев. По своей точности метод вполне сопоставим с радиолокацией или рентгенографией, так как используемая им аппаратура фиксирует мельчайшие изъяны целостности стыка.
Поэтому он является наиболее доступным и результативным поточным способом. Но сфера использования ультразвуковой дефектоскопии сводятся к геометрическим параметрам заготовки, которая исследует сварные швы трубопроводов высокого давления.
Сущность понятия
Ультразвуковой контроль сварных швов базируется на физических основах волновой системы, которая отталкивается от стыка различных сред. Никакого вреда организму человека этот метод диагностики не приносит.
Диапазон данного вида неразрушающего контроля составляет от 20 кГц до 500 МГц. Направленные от источника однородные сигналы двигаются с равномерным ускорением. При изменении среды происходит их преломление или отражение. Продольные волны обладают скоростью почти вдвое большей, чем поперечные.
Тонкость настройки оборудования связана с ее конструктивными особенностями. Посредством ультразвукового контроля сварных швов определяются включения, зерна, лакуны, примеси, раковины, которые уменьшают прочность соединения.
Достоинства и минусы дефектоскопии
Преимущества такого метода заключаются в:
- безопасности для человека;
- высокой надежность диагностики с выявлением большинства изъянов;
- мониторинге качества сварных швов, когда не нужно отделять кусок металлоконструкции для лаборатории;
- оперативности при определении состояния стыка, ускоряющей результат;
- универсальности;
Недостатками метода становятся ограничения использования и потребность в подготовке профессионалов.
Ультразвуковая волна быстро затухает при контакте со структурами крупнозернистого характера. Поэтому здесь следует применять преобразователи с особым радиусом кривизны.
Типы и способы контроля
Для осуществления УЗД соединений применяют техники прямого луча, а также двукратного, многократного или однократного отражения.
Вектор сигнала выбирают, используя нормаль, где угроза дефектов велика. Наиболее распространенными видами измерений являются:
- эхо-импульсная диагностика, когда устройство формирует волну и настраивается на ее отклик. Если он улавливается, то в материале имеется разделение сред;
- эхо-зеркальный контроль посредством генерирующей волны датчика и улавливающего ее приемника. Ось соединения находится под углом к устройству. Приемник находит дефекты, фиксируя УЗ-сигналы;
- теневой способ, когда волны расходятся по поверхности соединения. Если сигнал отражается и улавливается приемником, находящимся за сварным швом, то возникает тень;
- зеркально-теневой действует с помощью комплекта датчиков, улавливающих сигналы колебаний. Чистая волна означает, что стык безупречен;
- дельта направляет определенную волну, отражение которой обнаруживает дефекты соединения. При необходимости высокоточных результатов прибегают к тонкой настройке.
В практической деятельности ультразвуковая дефектоскопия находит изъяны сварки посредством теневых и эхо-импульсных методов. Способ неразрушающего контроля помогает отыскивать поврежденную часть, которая грозит разгерметизацией сварного соединения.
Так осуществляют профилактику аварий, особенно на трубопроводах с повышенными требованиями прочности.
Методика осуществления и сфера использования
Ультразвуковой контроль сварных швов применяется при мониторинге легированной и углеродистой стали, стыков сварки цветного металла и чугунных изделий.
Контрольные устройства обнаруживают:
- изменение геометрии в отдельных местах;
- наличие посторонних включений и другие нарушения структуры;
- необработанные участки;
- созданную газом из атмосферы пористость;
- обвисание диффузности при разломе;
- различные расслоения;
- ржавчину внутри застывшего расплава;
- сквозные изъяны швов;
- складчатость из-за наплава и др.
УЗК позволяет отслеживать следующие виды соединений конструкций:
- кольцевые, трубные или фланцевые;
- любые сложные варианты;
- поперечные и продольные, испытывающие повышенное давление или нагрузки;
- тавровые.
Когда звуковой сигнал проходит сквозь решетку из металла, то он рассеивается, создавая сложности при использовании техники.
Геометрические ограничения:
Контролируемые заготовки не должны быть толще 50-80 см или тоньше 8-10 мм;
расстояние до исследуемого объекта должно составлять по меньшей мере 3 мм, максимально – 10 м.
УЗД великолепно проявила себя в производстве автомобилей, строительной области и на заводах, оснащенных трубопроводами повышенного давления.