Методы контроля сварных соединений
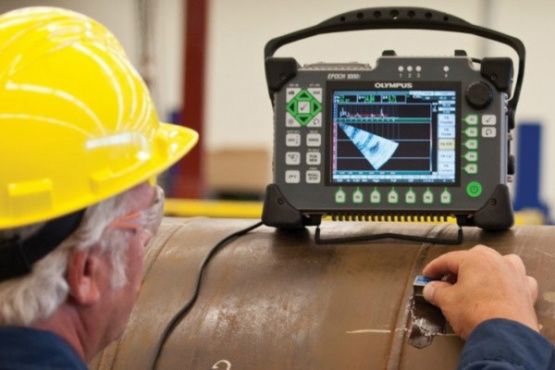
Работоспособность конструкции, выполненной сварным методом, целиком зависит от качества сварных швов. Дефекты снижают механические характеристики изделия и могут привести к его разрушению. Проницаемость швов ухудшает герметичность работающего под давлением оборудования. Методы контроля сварных соединений разделяются на разрушающие и неразрушающие.
К наиболее используемым методам неразрушающего контроля относятся:
- внешний визуальный осмотр;
- радиационная дефектоскопия (радиографический метод);
- магнитный контроль;
- ультразвуковая дефектоскопия;
- капиллярная дефектоскопия;
- контроль швов на проницаемость;
- контроль с использованием вихревых токов.
Визуальный осмотр
Контроль сварных соединений всегда начинается с внешнего осмотра, позволяющего выявить наружные дефекты и часть внутренних. Выявляются дефекты, подобные геометрическим отклонениям шва (отличиям в высоте и ширине шва, катета), неравномерному распределению складок, что свидетельствует о непроварах вследствие обрывов сварочной дуги.
Путем внешнего осмотра выявляются также поверхностные поры и трещины, подрезы и наплывы. Перед осмотром следует очистить швы от технологических загрязнений – шлака, окалины и брызг металла (шкрапа). Мелкие недочеты становятся виднее при предварительной обработке поверхности спиртовым раствором, а затем 10%-раствором азотной кислоты (с последующей очисткой кислоты спиртом после браковки).
Капиллярный контроль
Данный способ позволяет проверить сварные конструкции из любых материалов, любой формы и размеров. Основан способ на возможности некоторых жидкостей с малым поверхностным натяжением проникать сквозь малейшие трещины (капилляры) внутрь материала изделия. Метод выявляет невидимые невооруженным глазом или через лупу поверхностные дефекты.
Логическим продолжением капиллярного метода является метод контроля качества сварки на проницаемость. При контроле сварных соединений этим методом необходимы особые вещества, называемые пенетрантами, которые проникают внутрь сварного шва сквозь поверхностные дефекты и окрашивают нарушения в яркий свет.
Одним из эффективных и недорогих пенетрантов является керосин, мгновенно заполняющий все канавки, поры и прочие мелкие дефекты. Протечки керосина через сварной шов проявляются как темные пятна или полосы на покрытии шва из мела или белой глины (каолина). Немедленно после нанесения керосина следует осмотреть обратную сторону шва. Точки указывают на наличие свищей и пор, а полоски – сквозных трещин.
Проверка швов на проницаемость
Проверке швов на проницаемость подлежат сосуды и системы, к которым предъявляются требование герметичности. Подобные сосуды испытываются посредством следующих способов:
- течеискание;
- пузырьковый метод;
- пневмоиспытание;
- гидроиспытание.
Магнитная дефектоскопия
Метод основан на свойствах магнитных силовых линий реагировать на изменения в толще металла, подобная проверка возможна лишь на ферромагнитных материалах. Немагнитные материалы, к которым относятся медь, алюминий и хромоникелевые стали, данному методу контроля не поддаются. Создаваемое вокруг проверяемой области магнитное поле искажается в местах дефектов.
Для фиксации искажений поля применяются магнитопорошковый, магнито-индукционный либо магнитографический методы. При подобной проверке на поверхность сварного шва наносится сухой либо в смеси с мыльным раствором, маслом или керосином ферромагнитный порошок (например, железная окалина либо окислы железа), который концентрируется в местах дефектов. Намагничивается изделие электромагнитом или пропусканием через изделие электрического тока.
Ультразвуковая дефектоскопия
Ультразвуковая дефектоскопия - один из самых распространенных способов проверки качества сварного шва, и считается самым удобным. Используется способность ультразвуковых волн отражения от разделяющей две среды с отличающимися акустическими свойствами границы.
Проходящие через металлическое изделие ультразвуковые волны, испускаемые ультразвуковым источником, отражаются нижней поверхностью изделия и фиксируются датчиком дефектоскопа, который отображает искажения волны вследствие наличия дефектов. Природа изъяна определяется по характеру отражения, при этом выявляются изъяны как поверхностные, так и глубинные.
Ультразвуковые дефектоскопы дают пользователю весьма специфические, трудно поддающиеся расшифровке данные. Провести качественный контроль сварных соединений этим методом способен лишь обученный этому специалист. Другой недостаток ультразвуковой дефектоскопии – ограниченность применения на чугуне, аустенитных сталях и прочих материалах с крупным зерном.