Методы дефектоскопии металлов и сплавов: применение и плюсы ультразвука, магнитопорошка
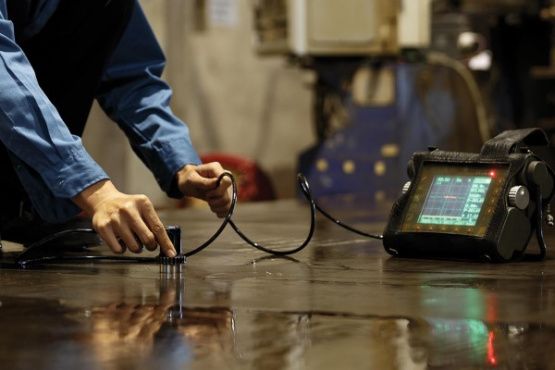
Дефекты в металлах, сплавах появляются по причинам несовершенства технологии производства деталей, интенсивной эксплуатации механизмов и выражаются в нарушениях однородности массы предметов, их структуры. Выявляют отклонения в целях предотвращения аварий, как следствия изменившихся характеристик материала: плотности, упругости, электропроводности. Дефектоскопия используется для проведения контроля качества металлоизделий методами неразрушающего контроля при воздействии на объекты исследований облучением, радиоволнами, ультразвуком (УЗ), магнитным и иными полями.
Применение и плюсы ультразвуковой диагностики
Основатель метода – советский учёный Сергей Яковлевич Соколов, изучавший акустические колебания высокой частоты: 0,5-25 МГц. В 1928 году физик создал промышленный образец широко применяемого сегодня прибора ультразвуковой дефектоскопии.
Принцип действия аппарата основан на способности высокочастотных волн проходить сквозь металл без поглощения и отражаться от грани раздела веществ. Поток лучей при встрече с границей шлакового микровключения, трещины отчасти возвращается, а по интенсивности процесса определяют параметры обнаруженных дефектов. Входящий в состав аппарата генератор вырабатывает электроимпульс высокого напряжения для последующего преобразования датчиком в УЗ-волну. Передача сигнала на металл идёт через воду или гель, а отражённый трещиной, неоднородностью импульс обратным порядком высвечивается на дисплее прибора. Промышленность выпускает УЗ дефектоскопы непрерывного излучения пучка микроволн и импульсные.
Ультразвуковая дефектоскопия применяется при контроле швов сварных соединений, целостности деталей авиационных двигателей, стенок трубопроводов, сосудов высокого давления, железнодорожных рельсов. Выявляются дефекты, находящиеся в толще металла. С помощью ультразвуковых исследований в металлических элементах замеряют глубину цементации или закалённого слоя, определяют иные физические величины: плотность, модуль упругости, внутренние напряжения. Относительно иных методов неразрушающего обследования УЗ способ имеет ряд преимуществ:
- повышенная чувствительность к трещинам, непроварам швов;
- безопасность для оператора в сравнении с диагностикой рентгеновскими лучами;
- возможность контроля в местах установки обследуемого объекта без ущерба технологическому процессу;
- допустимость проверки неметаллических элементов;
- низкая затратность диагностики.
Недостаток УЗ-дефектоскопии – невозможность определить истинные размеры каверн, трещин при проверке металлов с крупнозернистой структурой. Трудности обусловлены затуханием ультразвука. Другой минус – повышенные требования к контролируемой поверхности в части шероховатости, волнистости.
Магнитная дефектоскопия
Метод основан на способности ферромагнитных металлов (Fe, Со, Ni), их сплавов с иными металлическими элементами намагничиваться. Условие применения способа – выход дефекта на поверхность детали или нахождение трещин, волосовин (флокен), несплавлений, неметаллических вкраплений, на глубине <3 мм. Исследования проводятся при изготовлении деталей, а также для обнаружения усталостных трещин.
Для магнитной диагностики часто используется магнитопорошковый метод дефектоскопии. Содержание обследования: деталь намагничивается, затем покрывается мелкодисперсными магнитными частицами в сухом виде или суспензией – смешанными с керосином, маслом или водой. Песчинки ферромагнитного порошка в зоне намагничивания ориентируются по силовым линиям поля: они огибают разрывы, отмечают рисунком контуры дефекта металла.
Преимущества магнитопорошкового метода дефектоскопии:
- видимость нарушений структуры невооружённым глазом: по феррочастицам фиксируются и узкие микротрещины;
- малая трудоёмкость при хорошей скорости исследований – магнитный дефектоскоп применяется для массового контроля качества;
- возможность определения дефектов в приповерхностном слое детали, на её наружности;
- приметность полых каверн и заполненных иным веществом несплошностей.
Расшифровку полученных индикаторных рисунков проводят визуально или с применением декодера изображения. После осмотра испытанную деталь размагничивают.