Дефекты сварных швов: разновидности, причины образования, методы выявления и контроля
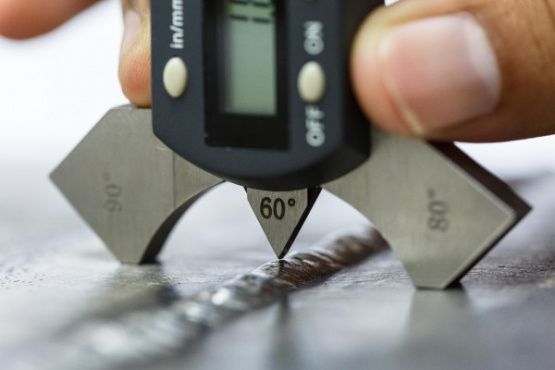
Сварка металлов – надёжный способ соединения деталей. Недоработки приводят к ослаблению сварочного шва, влекут снижение безопасности, срока службы конструкции.
Дефекты сварных швов
Описание, классификация изъянов сплошности в металлических материалах при сварке плавлением приведены в стандарте ГОСТР ИСО 6520-1-2012, заменившим ГОСТ 30242-97. Металлургический брак документом не рассматривается. Группируются дефекты по 6 основным видам:
- Трещины – наиболее опасное нарушение, способствует быстрому разрушению стыка, сооружения в целом, что может привести к трагедии. По размеру различают микро- и макротрещины, по направлению – продольные, поперечные, радиальные.
- Полости. Поверхностные называют свищами, они опасны предрасположенностью к развитию трещин. Форма произвольная, образовываются на любой стороне: внешней, внутренней. Другая разновидность полостей – поры в массе свариваемого соединения.
- Включения твёрдые: шлаковые, флюсовые, оксидные и другие.
- Непровар, несплавление. Наблюдаются между швом и телом металла, который не достиг температуры плавления. Прочностные характеристики при этом понижаются.
- Нарушения формы, размера. Выражаются в подрезах, кратерах. Первые видятся углублением снаружи шовного выступа: сечение шва уменьшается, прочность соединения падает. Второй дефект – небольшие углубления в сварном валике. Дно кратера рыхлыми включениями может провоцировать образование трещин.
- Прочий брак. Наплыв – ложный валик расплава, не сплавившийся с рабочей поверхностью. Прожог – сквозное отверстие от вытекания металла из сварочной канавки.
Дефектные участки выявляются контрольным осмотром. Могут быть следствием недоработок при подготовке сварочных работ, ошибок сварщика.
Причины возникновения изъянов
Процесс сваривания металлов предполагает применение разных технологий, оборудования, материалов. Участники техпроцесса должны обладать знаниями и умением их применять. Факторы, влияющие на качество производства сварочных работ, причины дефектов:
- Применение недоброкачественных расходных материалов, неправильное их сочетание приводят к образованию трещин. Высокое содержание углерода в присадке – источник появления пор в соединении. Избыток присадочной смеси на кромках стыка вызывает наплывы.
- Нарушение технологии сварки. Излишние нагрев, охлаждение металла способствуют трещинообразованию, появлению наплывов. Завышенный ток приводит к подрезам, разрыв дуги – к образованию кратеров, а впоследствии – к трещинам.
- Неисправность оборудования. Неправильное расположение стыков повлечёт растрескивание шовного валика.
- Низкая квалификация сварщика, оператора автосварочной установки. Загрязнение заготовки, быстрая проводка электрода – причины непроваров, образования пор в структуре сварного соединения. Замедленное перемещение, большой ток приводят к прожогам.
Точное соблюдение технологических параметров, регулярная переаттестация специалистов, контроль качества используемых материалов помогут избежать брака при сварочных работах.
Методы выявления недоработок при сварке
Самый доступный способ обнаружить дефектные места сварного шва – внешний осмотр. При этом может использоваться лупа до 10-кратного увеличения, мерительный инструмент. Основные методы неразрушающего контроля:
- Визуальное определение изъянов, или визуально-измерительный контроль. Выполняется после предварительной очистки поверхности от шлака, окалины, застывших брызг металла. Отыскиваются прожоги, трещины, свищи, производятся замеры кратеров.
- Испытания на герметичность сварных сосудов, трубопроводов. Поры, непровары, трещиноватость выявляются обработкой керосином и мелом, заполнением участка труб водой под напором, обдуванием воздухом.
- Приборный поиск брака. Используются радиационные лучи, ультразвук, магнитное поле. Для открытых изъянов применяют люминесцентный метод.
Испытательная лаборатория производит контроль качества сварки обследованием стыка и околошовной зоны на всём её протяжении с сохранением целостности конструкции, а также испытывает образцы на прочность. Диагностика позволяет определить характерные параметры дефектов, рекомендовать меры по устранению недоработок.
Разрушающий контроль сварочных работ
Для проведения этого вида обследований отбираются контрольные образцы соединений, вырезанных на проверяемых участках. При испытаниях определяют прочность сварного шва, зоны температурного воздействия. С помощью исследований устанавливают:
- правильность подбора флюса, проволоки, иных материалов;
- нарушения технологии по параметрам: скорость проводки электрода, сила тока;
- профессиональные навыки сварщика, оператора автосварочного агрегата.
Методы разрушающего контроля: проведение химических анализов, механические испытания на твёрдость, разрыв, статический и ударный изгиб. Металлографические исследования позволяют увидеть дефекты и структурные изменения от термического, электрического воздействия на макро- и микрошлифах.